Different track link designs and configurations can have a significant impact on the performance of an excavator.
Here are some ways in which they can affect the machine:
Traction and Stability: The design and configuration of track links influence the excavator’s traction and stability. Wider track links with larger surface areas provide increased contact with the ground, resulting in improved traction, especially in challenging terrain conditions. This enhances the machine’s ability to maneuver and work efficiently.
Ground Pressure: The design of track links can affect the distribution of weight and the ground pressure exerted by the excavator. Some track link designs distribute weight more evenly, reducing ground pressure and minimizing the risk of sinking or damaging the ground surface. Lower ground pressure is particularly beneficial when working on soft or fragile surfaces.
Durability and Wear Resistance: The design and material composition of track links impact their durability and resistance to wear. Different designs may incorporate features like reinforced edges, hardened surfaces, or special coatings to enhance their wear resistance and extend their lifespan. This is particularly important in demanding applications or when operating in abrasive environments.
Noise and Vibration: Track link designs can have an influence on noise and vibration levels generated during excavator operation. Some designs incorporate noise reduction features, such as rubber pads or damping elements, to minimize the noise and vibration transmitted to the operator and surrounding environment. This can improve operator comfort and reduce noise pollution on job sites.
Track System Efficiency: The design and configuration of track links can impact the overall efficiency of the excavator’s track system. Some designs offer reduced rolling resistance, allowing the machine to move more smoothly and efficiently. This can result in improved fuel efficiency and reduced operating costs.
Maintenance and Serviceability: Track link designs may vary in terms of maintenance requirements and ease of serviceability. Some designs are specifically engineered for easy track link replacement, reducing downtime and maintenance costs. Additionally, features like self-lubricating components or sealed track link systems can minimize the need for frequent lubrication and maintenance.
It’s important to note that the specific impact of track link designs and configurations can vary depending on the excavator model, manufacturer, and intended application. Manufacturers typically provide recommendations and guidelines for selecting the appropriate track link design based on factors such as machine weight, operating conditions, and job site requirements. Considering these factors and working closely with the manufacturer can help optimize the performance of an excavator’s track system.
How are excavator track links connected to form a continuous track system?
Excavator track links are connected to form a continuous track system through the use of track pins and bushings.
Here is a step-by-step process of how the track links are connected:
Track Link Design: Each track link consists of two main components: the track shoe and the link assembly. The link assembly typically has holes or bores at each end to accommodate the connection with other track links.
Alignment: The excavator is positioned on a flat surface, and the track frame is leveled to ensure proper alignment of the track links.
Track Pin Insertion: A track pin is inserted through the aligned holes in the end of one track link. The pin is typically made of high-strength steel and has a head on one end and a threaded portion on the other.
Bushing Placement: A bushing, which is a cylindrical metal sleeve, is placed between the two track links. The bushing acts as a bearing surface and provides a smooth rotation between the track links.
Link Assembly Connection: The track pin is inserted through the second track link, passing through the bushing. The threaded end of the pin extends beyond the track link.
Threaded Nut Installation: A threaded nut is then screwed onto the threaded end of the pin. The nut is tightened using specialized tools or equipment to secure the track link assembly.
Torque Application: Once the nut is tightened, the track pin is torqued to the manufacturer’s recommended specifications. excavator track links in China This ensures that the connection is secure and prevents the track links from coming apart during operation.
Repeat the Process: The above steps are repeated for each subsequent track link until the desired track length is achieved. The number of track links required depends on the size and configuration of the excavator.
Final Inspection: After the track links are connected, a thorough inspection is conducted to ensure that all connections are properly made, and there are no loose or damaged parts. This is important for the safe and efficient operation of the excavator.
It’s worth noting that the specific process of connecting excavator track links may vary slightly depending on the excavator model and manufacturer. Proper installation and maintenance of the track links are crucial to ensure the integrity and performance of the excavator’s track system. Regular inspections and timely replacement of worn or damaged track pins, bushings, and other components are essential for optimal track system operation.
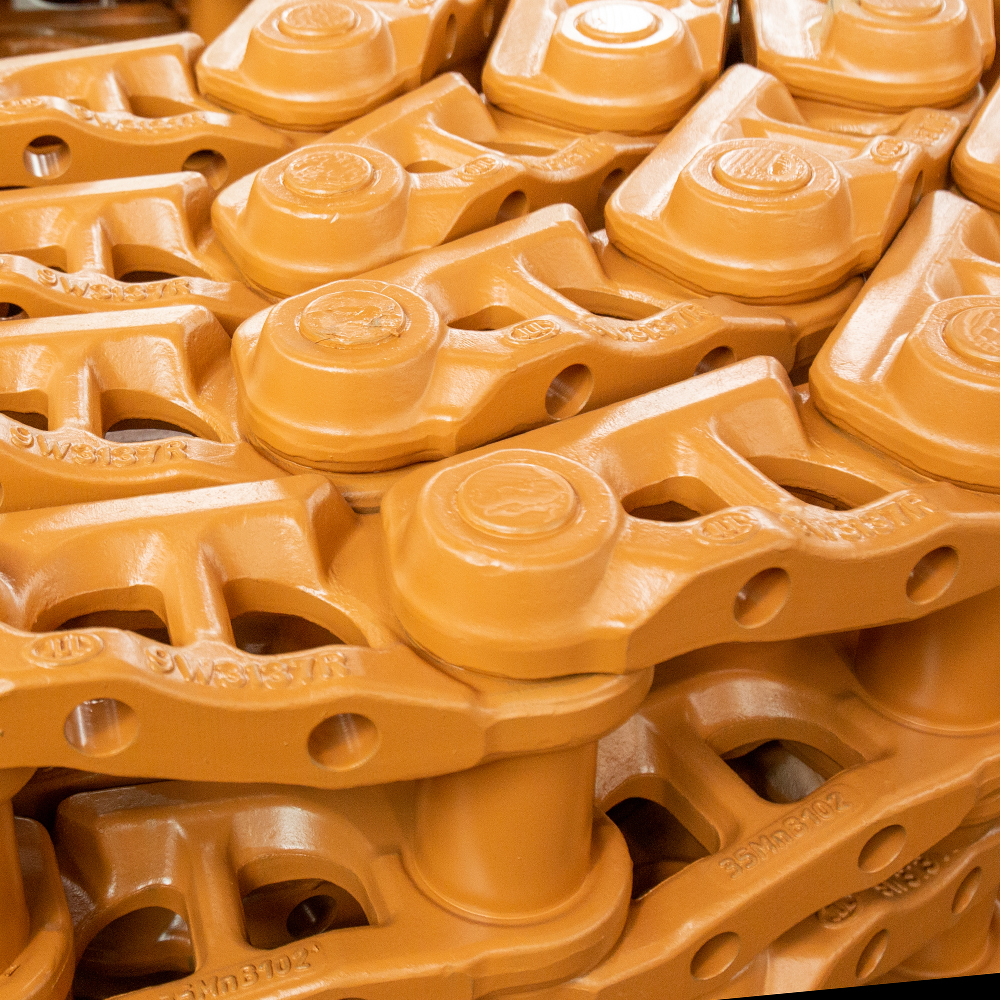